リーマは再研磨できないの!?リーマを廃棄せずに使いこなす方法とは?
リーマの精度は1/1000mm単位で寸法指定されたものであり、とても精密な刃物です。
一般的なリーマはドリルであけた穴を仕上げるために使用される切削工具で、リーマとドリルはセットのようなものです。
しかし、それらの刃物の切れ味が落ちると、ドリルは再研磨して再利用する一方で、リーマはその高精度の印象もあってか再研磨できない、もしくは再研磨後の精度が落ちるからという思いから使い捨てにしてしまう、そんなことがあるのではないでしょうか。
またその精度ゆえに、そのリーマを製作した工具メーカーでないと外径保証ができないから、多少のコストがかかっても工具メーカーに再研磨依頼をしている、ということもあるのではないでしょうか。
弊社内の機械加工部門で使用しているリーマは、刃径4~12mmと数種類のものを使用していますが、100%再研磨でリサイクルしています。また当社では様々な工具メーカーの超硬・ハイスリーマを数多く再研磨しています。
リーマは高価な工具なので、再研磨しない手はないです。しかしリーマの再研磨は、ドリルやエンドミルと比較して数は少ないと感じております。そこで今回は、リーマという工具と加工方法から、バックテーパーを考慮したリーマの再研磨やリサイクル方法について、まとめて解説いたします。
リーマとは
リーマはドリルなどで開けた穴に通すことで穴の真円度や円筒度、加工面や寸法精度を高める切削工具です。リーマには穴を開ける機能はなく、必ず事前に開けた穴に使用しなければなりません。
また、似た名称の工具としてバニシングリーマがありますが、バニシングリーマはリーマのように底刃はなく、下穴がないと使えません。
>>バニシングリーマやバニシングドリルとリーマの違いは何ですか?
また、リーマ加工の流れは下記の通りです。
1.まずは、仕上げたい穴径のリーマを選定します。
2.リーマで仕上げたい最終穴径よりも小さいドリルで下穴をあけます。下穴の最適な径サイズは、素材や径の大小によって一概にいえませんが、リーマ径より0.2~0.5mmほど小さい下穴になるようにします。
3.実際にリーマで加工を進めていきます。
リーマは1000分の1mmの単位で径指定ができるほどとても精密なものです。ドリルを使った時に振られたりして穴径が大きくなってしまうことがありますが、それはリーマでも起こることですし、精密な加工をするリーマには小さな振れが大きな問題となってしまうこともあります。
リーマの再研磨
リーマの再研磨は、エンドミルのように外刃を研磨してしまうと外径が変わってしまい、加工穴の寸法が変わってしまうため、外径の再研磨はしません。使った分の刃長をカットして、先端コーナーの食い付き刃を再刃付けします。
食い付き刃であっても角度の多少のバラつきなどがあると、加工精度も落ちるため、再研磨する装置は安定したもので振れがないことを確認してから刃付けします。
>>リーマを再研磨するタイミングとは? リーマの寿命を延ばすための6つのポイントとは?
リーマの刃長が短くなると起きること
再研磨は使用した刃長をカットします。そのカットする長さやそのリーマ自体の規格にもよりますが、刃長が短くなるとリーマの径は細くなります。エンドミルやドリルも共通のことですが、それはリーマにも外周刃にバックテーパーが付いているからです。
JISによると
「直径Dには,原則として長さ100mmにつき0.03mmのバックテーパを付けることが望ましい。」
とあり、この数値から角度は約0.009度で、刃長5mmでは径約0.0015m、刃長10mmでは径0.003mmといった具合で径が細くなる計算になります。
また、刃長が短くなるとリーマの剛性も上がり倒れ等が小さくなるため、新品の時よりもバックテーパーの影響がないとしても径は小さくなる傾向にあります。
そのためリーマについては、実際に再研磨してみて何回使ったら(刃長何回分落としたら)加工時にどれくらい寸法が変わるか把握しておくことが大事です。
本来の目的とは違いますが、バックテーパーで細くなってしまうのを補うために、コーティングで径を太らせる方法もありです。コーティングの膜厚は1~5/1000㍉など種類によってあり、膜厚で調節することも可能です。
>>リーマを再研磨するタイミングとは? リーマの寿命を延ばすための6つのポイントとは?
リーマは工具メーカーでないと再研磨できない?
先述の通り、リーマはその精度ゆえに、「このリーマを製作した工具メーカーでないと外径保証ができないから、多少のコストがかかっても工具メーカーに再研磨依頼をしている」、というお声も耳にしたことがあります。
しかし実際には、リーマは外刃を研磨してしまうと外径が変わってしまい、加工穴の寸法が変わってしまうため、外径の再研磨はしません。使った分の刃長をカットして、先端コーナーの食い付き刃のみを再刃付けします。そしてこれは、工具メーカーであっても同じことです。
そこで大切なのは、リーマの同心性です。つまり、工具メーカーであっても再研磨業者であっても、リーマは食い付きのみのため再研磨で品質には大きく影響なく、ただ同心性について保証可能な業者に再研磨すべき、とも言えます。
当社では、リーマの再研磨前後で同心性の測定も行っているため、品質の高いリーマの再研磨に対応可能です。
また再研磨.comでは、ドリルやエンドミル、リーマ等の切削工具を高い品質で再研磨するため、最新の加工設備や検査設備を取り揃えています。当社の再研磨は、職人が手作業で行う再研磨とは異なり、繰り返しの精度が高い、安定した品質での再研磨加工を可能としています。
さらに当社では、再研磨のコストメリットも強みの1つであると考えております。一般的に工具メーカーでは、あくまでも工具製造が主事業のため、工具の再研磨は比較的価格を高く設定しているケースが多く見られます。一方で当社は再研磨のみで事業を展開しており、また様々なメーカーの工具を再研磨しているため、技術と実績を兼ね備えた上で、小回りの利いた低コストで高品質な再研磨サービスを展開しております。この当社ならではの再研磨を評価いただき、現在では非常に多くの方々に全国各地から工具再研磨のご依頼をいただいております。
リーマは再研磨だけでない!リーマを廃棄せずに使いこなす方法とは?
超硬素材の材料はレアメタルを使用しており、近年はその価格も高騰しています。直径が16mm以上の超硬工具になると、材料費だけでも数万円もしてしまいます。
もし、これから新規で用意する刃具がある場合は、使っていない超硬工具を材料として再利用できればコストを抑えることができます。
例えば、当社で多いのはバニシングリーマや、バニシングドリルの製造です。段付きのバニシングリーマやバニシングドリルは、ほとんどの場合が加工製品の寸法に合わせて作る特注品であるため、通常の既製品の刃具よりも高価になります。
そのため、リサイクルのよくある事例としては、使わなくなった超硬工具を段付きのバニシングリーマやバニシングドリルに作り替えるということがよく行われています。
では、どのようなリーマであればリサイクルできるのでしょうか。ここには大きく2つのポイントがあります。
・新しく作る刃具径がリサイクル元の工具の径以下であること
・リサイクル元の再利用可能な長さが、新たに作る刃具の溝長、ツールホルダーにセットする長さ、さらに刃具作成のときに砥石が干渉しない長さが必要
>>どのような超硬リーマならリサイクルできる?リーマのリサイクル事例もご紹介!
リーマの再研磨事例
続いて、実際に当社が行ったリーマ再研磨事例をご紹介いたします。
【リーマφ2.993の再研磨】
こちらは当社で手掛けた、Φ2.993の4枚刃リーマの再研磨事例の一つです。
使用した長さをカットして食い付きを再刃付けしています。
【リーマφ4の再研磨】
こちらは当社で手掛けた、Φ4の4枚刃リーマの再研磨事例の一つです。
使用した長さをカットして食い付きを再刃付けしています。
【リーマφ4.975の再研磨】
こちらは当社で手掛けた、Φ4.975の6枚刃リーマの再研磨事例の一つです。
使用した長さをカットして食い付きを再刃付けしています。
【リーマφ12の再研磨】
こちらは当社で手掛けた、Φ12の6枚刃リーマの再研磨事例の一つです。
使用した長さをカットして食い付きを再刃付けしています。
リーマのリサイクル事例
続いて、実際に再研磨.comで行ったリーマのリサイクル事例をご紹介いたします。
リーマリサイクルの事例①:スパイラルリーマ改造で3工程を1工程に集約した工具改造事例
ひとつの穴を完成させるのに、3つのドリルを必要とするため、3工程が必要で、さらに切削機に取り付けられるツールの数に限りがあり、出来るだけ工程集約がしたかったということで、再研磨.comにご相談をいただきました。
再研磨.comでは、スパイラルリーマの外径を細くして2段化し、刃先に45°の角度をつけて、面取りも可能な段付き(2段)のリーマに改造することを提案いたしました。
リーマリサイクルの事例②:リーマの先端を90度底刃付に改造して、3工程集約、作業時間1/3に成功した工具改造事例
穴を開ける作業で、穴径、穴加工精度の基準が厳しいため、センタードリル、下穴ドリル、リーマ加工の3段階に分けて加工をしていたとのことです。しかし、穴開け作業のために3本の刃具を取り換えながら用いていたため、とても作業効率が悪く、生産性を上げたいとのことで再研磨.comがご相談を受けました。
再研磨.comでは、ストレートリーマの先端を90度に切り先端に刃先を付けて、90度底刃付リーマに改造することを提案いたしました。
リーマリサイクルの事例③:使用済リーマの刃先を改造して、面取りカッターにした工具改造事例
使用済の段付きリーマが手元にあったのですが、「超硬なので捨てるにはもったいない。何かに再利用が出来ないか。。。」と考えていらしたところ、再研磨.comにご相談をいただきました。
再研磨.comでは、使い切ったリーマの刃先部分を改造して、刃を付け直しすることを提案いたしました。これにより、使用済みリーマを面取り用カッターとして蘇らせました。
下記の動画では、ドリルとエンドミルの違いについて、アニメーション付きでわかりやすく解説していますので、ぜひご覧ください!
このほかにも再研磨.comでは、ドリルやエンドミルの再研磨に関する情報発信を行っております。ぜひご覧ください!
ドリルに関する記事はこちら
>>ドリル寿命の判定方法とは?診断方法、寿命判別式までご紹介!
エンドミルに関する記事はこちら
>>【加工シーン別】エンドミルの2枚刃と4枚刃の使い分けについて解説!
>>エンドミルにねじれ角がある理由とは?直刃との違い、メリット・デメリットについて解説!
その他の記事はこちら
【再研磨の匠にしかできない技を、貴社の刃物に】
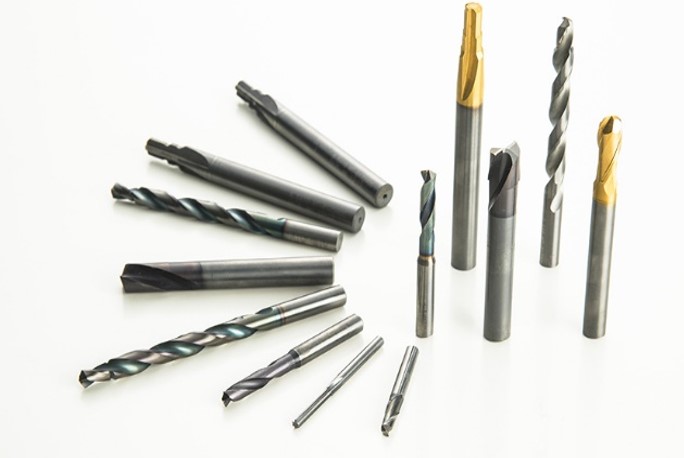
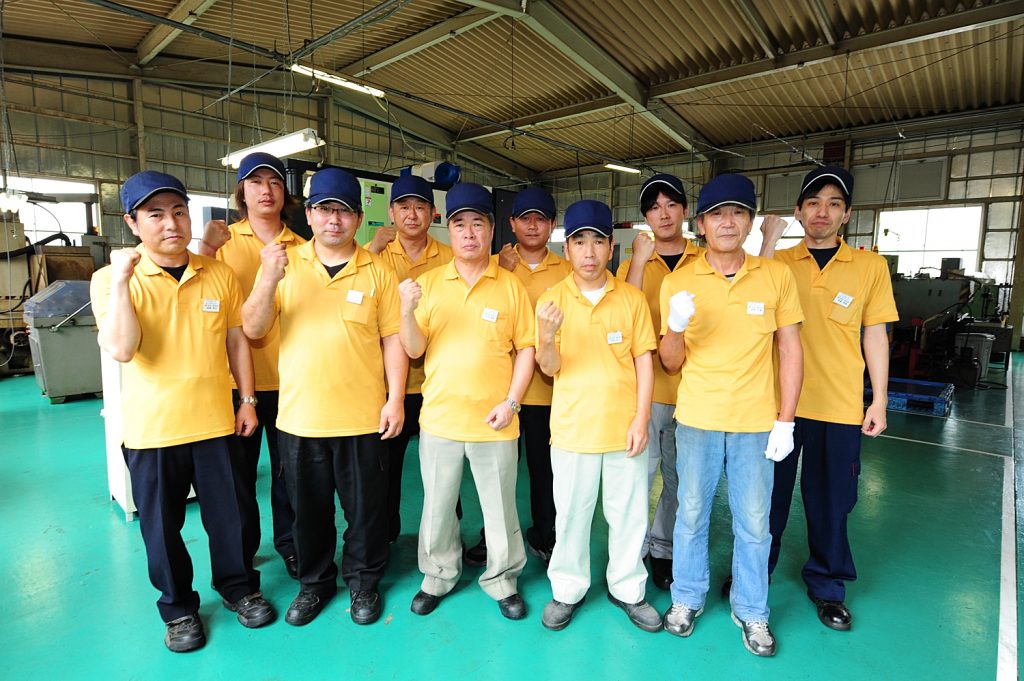
切削加工会社である当社が、片手間で行う事業ではなく、工具研磨専用の加工設備・検査設備を取りそろえておこなっている、本気の再研磨です。そのため、どこにも負けない品質で工具の再研磨加工を行うことをお約束いたします。当社は、「再研磨の匠にしかできない技を、貴社の刃物に。」を合言葉に、一本一本の再研磨に魂を込め、お客様を“工具”からサポートいたします。
ドリルやエンドミル、リーマなどの切削工具の再研磨を検討されている方は、まずは再研磨.comへお気軽にご相談ください。