【必見】超硬工具とハイス工具を使い分けるための9つのポイント
切削工具を使用している方は、超硬とハイスについて一度は悩んだことがあると思います。
超硬はハイスと比較して、購入価格も再研磨価格も高価になります。しかしそれでも、超硬工具のニーズは高いのも事実です。加工品質の向上やサイクルタイムの短縮、またコスト面でも長く使えば使うほど、超硬はハイスより有利になります。
ここでは、超硬工具とハイス工具を様々な面で比較し、工具を使い分けるためのポイントを9つにまとめてご紹介いたします!
超硬工具とハイス工具の徹底比較!
コスト:超硬工具はイニシャルコストが高い!
超硬:△
ハイス:〇
超硬の原材料は、レアメタルのタングステン、タンタル、結合剤としてコバルト等です。これらを混合した後に焼結して作られるのが超硬です。このように超硬は希少価値の高い材料を使用しているため、とても高価です。
一方、ハイスの原材料はタングステン、モリブデン、コバルト、クロム、パナジウム等です。
製法が異なる溶解ハイスと粉末ハイスがあり、粉末ハイスの方が溶解ハイスより耐摩耗性、じん性に優れています。
超硬工具は、径が太い物になると数万円と、とても高価なものになってしまうため、どうしてもφ16~20以上はハイス工具が多用されます。
硬さ・耐摩耗性:超硬はハイスの数倍も硬い!
超硬:◎
ハイス:〇
ハイスは鋼の中ではかなり硬い材料ですが、超硬はそのハイスよりも数倍硬い材料です。
更に、ハイスの耐摩耗性と耐熱性は、超硬より劣りますので、これらの点を理解し、他のメリットやデメリットを考慮した上で選定する必要があります。
靭性:断続切削向けのハイスと、脆く壊れやすい超硬
超硬:△
ハイス:〇
ハイスは粘りが強く、また振動にも強いため断続切削に向いています。また、切削中に強い力が加わると刃具は折れにくいですが、歪んだりして加工精度が落ちることがあります。
一方で超硬は硬いがゆえにもろい一面を持ち、強い衝撃が加わるとチッピングを発生させてしまいます。
再研磨:超硬は再研磨の工夫の必要あり、ハイスはホーニングの必要なし
超硬:すくい角、逃げ面、ホーニングなどで工夫の必要あり
ハイス:ホーニングの必要なし
超硬は硬くもろいため、すくい角や逃げ面をやや弱くして剛性を高めてあげる必要があります。例えばアルミ等では刃物を鋭利にするなど、ワークによっても再研磨の方法が変わります。また超硬の場合、ドリルの底刃などでは、ホーニング(ネガランド)を施すことで刃こぼれを大幅に減らすことができます。
一方、ハイスドリルではチッピングに強いため、ほとんどホーニングを施すことがありません。
砥石:超硬ではダイヤモンド砥石のため若干コストが△
超硬:ダイヤモンド砥石
ハイス:CBN砥石
再研磨で使用する砥石ですが、超硬はダイヤモンド砥石、ハイスはCBN砥石を使用します。超硬はその硬さゆえに、加工できるのがダイヤモンドなど超硬よりも硬度がある一部の材料に限られ、どうしてもコスト面ではハイスに軍配があがります。
コーティング:コーティングの種類が多彩なのが超硬の特徴
超硬:多彩な種類から、ワークにあわせて選定
ハイス:一部できないコーティングあり
超硬はもろく、ワークが硬いとチッピングや刃物自体が折れたりすることがあります。しかし、コーティングを施すことで強度を高めることができます。
コーティングは刃具の径にもよりますが数百円から千円前後ですが、コーティングひとつで「ここまで寿命が延びるのか!?」とびっくりすることがよくあります。(作業者である著者の感覚です。)
しかし、ワークに合ったコーティングを選択しないと効果が得られないこともよくありますので注意が必要です。たとえば、ワークがアルミニウムのときは、コーティングはダイヤにすると再研磨する必要がない程に寿命が長引きますが、金型材がワークの時に安いコーティングをしてしまうと、まったく効果がなくなってしまいます。
一方、ハイスにはダイヤのコーティングは施すことができません。その他にもハイスにはできないコーティング種類があります。
超硬工具とハイス工具の比較表
では、ここまでの超硬とハイスの比較をしてみましょう。
超硬 | ハイス | |
コスト | △ | 〇 |
硬さ | ◎ | 〇 |
靭性 | △ | 〇 |
再研磨 | すくい角、逃げ面、ホーニングなどで工夫の必要あり | ホーニングの必要なし |
砥石 | ダイヤモンド砥石 | CBN砥石 |
コーティング | 多彩な種類から、ワークにあわせて選定 | 一部できないコーティングあり |
このように、超硬には硬さやコーティングという面で非常に魅力のある特徴がある一方で、脆くコストが高いという繊細な一面もあります。一方でハイスは、無難に使うことができる工具材料であることがわかります。
超硬工具とハイス工具を使い分ける9つのポイント
では、超硬工具とハイス工具を使い分けるポイントを9つに分けて解説いたします。
断続切削:粘りが強いハイス工具が最適
断続切削は、切削が断続的になるため、工具に強い衝撃が何度もかかります。そのため、脆い超硬ではなく、ハイスの方が断続切削用の工具として最適であると言えます。
切削速度:耐摩耗性に優れた超硬で選択
切削速度が必要なワークの加工の時は、耐摩耗性に優れた超硬を選ぶ必要があります。そのため、アルミの加工でも超硬が使用されるケースが多くあります。
試作加工:お手頃なハイス工具でまずはトライ
試作加工をまずはやってみたい!というときは、あまりコストをかけずにまずはトライをするべきです。そのため、お手頃なハイス工具で試作加工をすることをおすすめしております。
量産加工:長く使える超硬工具の方が良い
一方で、ロット数が多くなる量産加工の場合は、様々なコスト面を考慮した上で、また品質精度も考慮した上で、工具のコストは高くなりますが超硬工具を選択するケースが多いです。
当社も焼結金属や圧粉磁心のような軟磁性体などの難削材の加工を多数行っておりますが、すべて超硬工具で対応しております。
加工精度:超硬の方が品質精度が良くなる
結局は品質精度が重要となる加工ですが、耐摩耗性や耐熱性という点でハイスよりも優れているため、良い製品を作ろうとした場合は超硬工具を選択する必要があります。
サイクルタイム短縮:超硬工具を使うと可能!
加工工程の始まりから終わりまでの時間を表すサイクルタイムですが、この短縮は生産管理において非常に重要な要素です。サイクルタイムの短縮は、結局は加工速度と相関関係にあるため、高い切削速度でも対応できる超硬工具であればサイクルタイム短縮が可能となるのです。
歩留まり向上:品質精度が良い超硬一択!
歩留まり向上を目指す場合も、やはり品質精度が良い超硬を選ぶ必要があります。
工具交換頻度の減少:超硬であれば長く使用することができる
超硬工具を使用すれば、耐摩耗性に優れているため、長く使用することができます。そのため、工具交換の頻度を抑えることができるため、リードタイム短縮につながり、生産のアウトプットに繋がっていきます。
生産コスト:超硬の再研磨をすれば、安く済む場合も…!
「でもコストならハイス工具一択か…」となるかもしれませんが、ここまでご覧いただければ、超硬の方が安く済む可能性もあるということがわかると思います。
超硬の優れた耐摩耗性により、そもそもが量産加工向けの工具材です。そこに再研磨やコーティング、ホーニングなどの工夫を重ねることで、ハイス工具を多数購入するよりも圧倒的にコストパフォーマンスが高くなるのです。
工具単体ではハイスの方が安くなりますが、生産コスト全体で比べると、実は超硬の方が安く済む場合が多く、これが超硬工具が広く利用されている理由です。
超硬工具とハイス工具を使い分けポイントまとめ
超硬 | ハイス | |
断続切削 | △ | ◎ |
切削速度 | 〇 | △ |
試作加工 | △ | ◎ |
量産加工 | ◎ | △ |
加工精度 | 〇 | △ |
サイクルタイム短縮 | 〇 | △ |
歩留まり向上 | 〇 | △ |
工具交換頻度の減少 | 〇 | △ |
生産コスト | 超硬の再研磨をすれば、安く済む場合も…! |
9つのポイントに分けて、超硬工具とハイス工具の使い分けについて説明してきました。
ハイスは粘り強く欠けにくく、振動に強いので断続切削に向いています。しかし、摩耗しやすく、高速切削には向きません。ただハイスは安価なので、試作品など数回使用するスポット的な加工であれば、お手頃なハイスの刃物を選ぶと経済的です。
一方、超硬は硬い一方で欠けやすいため、硬度の高いワークではコーティングをすると飛躍的にもちが良くなります。また耐摩耗性は高く、高速切削も可能なので量産品の加工に向いています。
これらのポイントを踏まえた上で、超硬工具とハイス工具を使い分けると、実際の加工に見合った工具選定ができると思います。
寿命がきた超硬工具とハイス工具を、捨てる&貯めるのはもったいない!
超硬やハイス製の工具は、非常に特殊かつ材料単価が高い工具です。一方、多くの企業が工具は使い捨てであると考えてしまって、廃棄してしまうもしくは棚にしまったまま…といったことが起きています。
工具を使い捨てと勘違いしたまま廃棄してしまうと、工具が摩耗する度に新しい工具を購入しなければならず、工具の購入コストがかさんでしまいます。また、もったいないと思ったまま使用済み工具を棚にしまったままにしていると、工場内で無駄なスペースをとってしまい、在庫管理面でコストがかさんでしまいます。
当社では、超硬やハイス等、様々なドリルの再研磨を行っております。その際に気になるのが、ドリルがどこまで使えるのか?というドリルの寿命についてだと思います。実際当社でも多くご相談をいただいておりますので、こちらの動画でわかりやすく解説しております!
再研磨.comが実際に行った、超硬工具の再研磨事例
それでは、実際に当社が行った超硬工具の再研磨事例のご紹介です!
事例①:刃先交換式エンドミルの再研磨事例
こちらはM社製刃先交換式のエンドミルの再研磨事例です。
深さ約5mmの溝加工に使用されており、使用した分の5mmをカットし、底刃を再刃付けしました。
エンドミルの寿命についてはこちら
>>【解説】エンドミルの寿命についてまとめました【判断項目一覧】
事例②:超硬製リーマの再研磨(エアロラップ処理)
こちらは当社で手掛けた、リーマの再研磨事例の一つです。
リーマは外周の再研磨はしないため、摩耗している部分の切り落とし、食い付きのみ再研磨します。
切削抵抗を抑えるため、コーティング後にエアロラップ処理を施しています。
リーマの寿命についてはこちら
>>【解説】リーマを再研磨するタイミングとは?寿命を延ばす6つのポイント
事例③:段付きバニシングリーマの再研磨(φ14-φ16)
こちらは当社で手掛けた、段付きバニシングリーマの再研磨事例の一つです。
3つのステップがあり先端が約φ14、シャンクがφ16になっています。
バニシング工具の寿命についてはこちら
>>【解説】バニシングドリル・バニシングリーマの寿命を判別する方法とは?
段付きドリルの寿命についてはこちら
>>【解説】段付きドリルの寿命を判別する方法とは?
公式LINE開設!再研磨で気になることをすぐに聞けて、簡単見積もりがさくさくできる!
再研磨 .comを運営する株式会社宮本製作所は公式LINEを運営しております!
こちらの記事をお読みの方で、下記のようなお悩みはございませんか?
「再研磨に関してちょっと気になることがあり、相談したい・・・」
「再研磨の技術について、もっと詳しくなりたい!」
「概算でいいので、すぐに見積もりを出したい・・・」
これらのお悩みを宮本製作所の公式LINEが解決いたします!
再研磨 .comの公式LINEでは「いつでもどこでも気軽に相談可能」と「さくさく簡単に見積もり診断可能」を主なコンセプトにコンテンツをお届けしています。
①いつでもどこでも気軽に相談
「この工具も再研磨できるのだろうか…」「再研磨すべきタイミングはいつなのか…」「サイトに掲載してある内容についてもっと詳しく聞きたい」など、ふとした疑問や日頃のお悩みをチャットにてお送りください!担当者より個別に回答させて頂きます。
②さくさく簡単に見積もり診断
LINE限定の機能として「見積もり診断」があります。「この工具を再研磨に出すといくらくらいかかるのかな、、、」といった疑問に対し大体の概算がLINE上でわかります!
更に詳細を知りたい場合は、個別対応も可能です。
工具の写真、型番、お見積りの本数をお送りいただくだけで、お見積りが可能です。
また、友達追加をしていただいた方限定で【再研磨1本無料サービス】をお届けします!
友達登録後にバナーが出てきますので、ご希望の方はクリックください。
お客様の再研磨に関するちょっとしたお悩み・ご相談、より簡単になった見積もり診断を中心に、再研磨に関するお役立ち情報を発信してまいります。
ぜひお気軽にLINEの友達追加をしてください!
※友達追加はQRコードを読み込んでいただくことで、10秒ほどで簡単に追加可能です。
>>今すぐ友達追加はこちらから
>>公式LINE詳細はこちらから
超硬工具の再研磨は、再研磨.comにお任せください!
再研磨.comを運営する株式会社宮本製作所では、焼結金属と呼ばれる非常に硬い素材の加工を行っており、その過程で得た加工に関するノウハウを活かし、工具の再研磨を行っています。
再研磨.comでは、ドリルやエンドミル、リーマ等の切削工具を高い品質で再研磨するため、最新の加工設備や検査設備を取り揃えています。当社の再研磨は、職人が手作業で行う再研磨とは異なり、繰り返しの精度が高い、安定した品質での再研磨加工を可能としています。
当社は、お客様が使用済みの工具を再研磨加工することで、刃物そのものの延命化を実現します。一般的に再研磨のコストは、工具購入コストの1/5~1/10程度です。そのため、お客様のコスト削減に大きく貢献することができます。
また、従来の切削では無理があった箇所を修正し、負荷を軽減することで、より多くの切削が可能となる刃物を提供します。ただ工具を再研磨するだけでなく、作業の効率化を図ることができる低コスト工具の提供を行っています。
さらには規格品よりも、高精度の加工をより少ない工程で加工を実現する工程集約工具への改造にも対応しています。
【再研磨の匠にしかできない技を、貴社の刃物に】
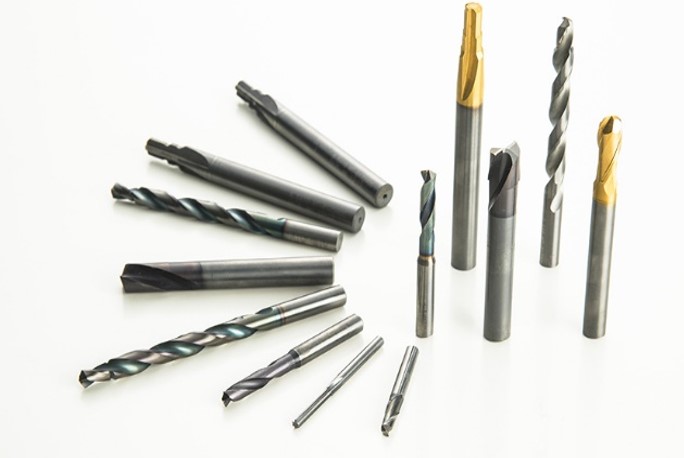
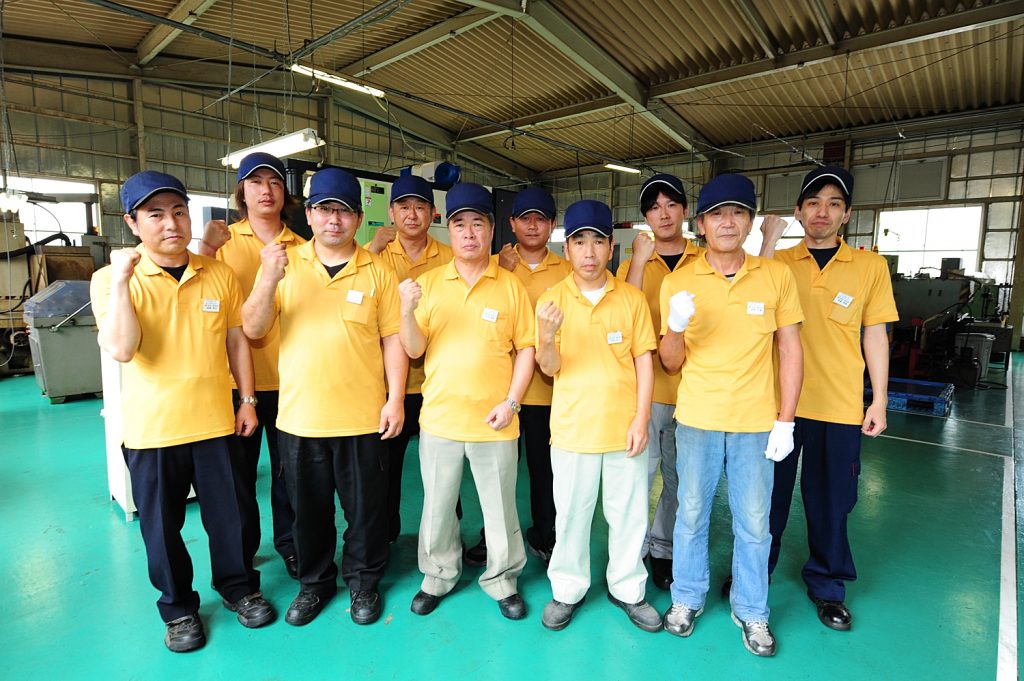
切削加工会社である当社が、片手間で行う事業ではなく、工具研磨専用の加工設備・検査設備を取りそろえておこなっている、本気の再研磨です。そのため、どこにも負けない品質で工具の再研磨加工を行うことをお約束いたします。当社は、「再研磨の匠にしかできない技を、貴社の刃物に。」を合言葉に、一本一本の再研磨に魂を込め、お客様を“工具”からサポートいたします。
ドリルやエンドミル、リーマなどの切削工具の再研磨を検討されている方は、まずは再研磨.comへお気軽にご相談ください。