エンドミルのアタリ付きとピン角は、どっちを選ぶべき?
再研磨.comでは、エンドミルの再研磨に関するご依頼を日々いただいておりますが、一部のお客様からは「ピン角でお願いします」という備考もいただいております。しかし、日常的にエンドミルを使用されている方々で、ピン角とアタリ付きを特段気にされている方は、あまり多くはいらっしゃらないようです。
当社では、お客様の加工しているワークの形状や材質、使用している工作機械、切削条件をお伺いした上で、エンドミルの形状変更に関するご提案も行っております。
今回はそのような提案活動の中で感じた、「エンドミルではアタリ付きとピン角のどちらを選ぶべきか」という疑問に、再研磨のスペシャリストがお答えします!
アタリ付きピン角とは?
スクエアエンドミルは大きく分けて「底刃」と「外周刃」から構成されています。さらにそれぞれの刃には「逃げ面」と「すくい面」があり、切れ刃を生成しています。
その底刃と外周刃が交わるコーナーでは、それぞれの逃げ面、すくい面からとても尖った状態になっています。
コーナーは鋭利であるため剛性が低く、加工で使用しているとまず最初に欠けなどが発生しやすい箇所です。
そのため、意図的にギャッシュを施す際に研磨砥石をコーナーに必要以上に当て、コーナーを落として剛性を高めるエンドミルの底刃形状を「アタリ付き」といいます。
逆にギャッシュを当てずに鋭利にした状態を「ピン角」といいます。
アタリ付きとピン角の違いとは?
エンドミルのアタリ付きとピン角の違いは、ギャッシュの位置です。
ギャッシュをコーナーに当てたものをアタリ付き、ギャッシュをコーナーに当てていないものをピン角と呼びます、
これはエンドミルの径方向の断面です。
ここにギャッシュを施すため、砥石を入れますが、その際にコーナー部に砥石を当てないと外周刃のすくい角がそのまま残ってピン角状態になります。また、コーナーに砥石をあてると外周刃のすくい角が落とされアタリ付き状態になります。
現物でのアタリ付きとピン角の見分け方
エンドミルの軸方向からみて外周刃のすくい角、つまり外周の丸い溝が底刃に見えるものはギャッシュがあたってないピン角といえます。しかし、外周のすくい角が小さかったり、エンドミルの径が小さかったりすると、目視では確認しにくいことがあります。
アタリ付きとピン角はエンドミルの径方向からも見分けることができ、ギャッシュが外周刃まで見えたらアタリ付き、ギャッシュが外周刃まで到達していないものはピン角となります。
アタリ付きとピン角の選択について
アタリ付きとピン角の大きな効果の差はコーナーの剛性にあり、アタリ付きの方が強度があります。
強ねじれのエンドミルは、切り屑の排出性の高さや外周刃と被削材との接触面が多くなり、場合によって有利な面があります。しかし、ねじれ角が大きいと底刃のすくい角も大きくなりコーナーの強度が落ちます。そのため、ねじれ角の大きいエンドミルはアタリ付きにすることが多いです。
しかし、アタリ付きは外周刃までギャッシュが延びているため、底刃にすくい角が無い状態になります。正確には、アタリ付きの場合でもまったくすくい角が無いわけではなく、ギャッシュに少し角度を付けて2~5度ほどのすくい角を付けますが、コーナーには外周のすくい角もなくなってしまいます。そのため、ピン角と比較するとアタリ付きではコーナー付近の切れ味は劣るため、非鉄材で切れ味を求める場合はピン角が最適となります。
また、アタリ付きはコーナー部に若干の寸法の差異が発生します。それは、ギャッシュでコーナーを落とすため、外周のすくい角がそのまま外周の切れ刃となるためです。その差異が発生する範囲と大きさは、エンドミルの径の大きさにもよりますがエンドミルの軸方向に約0.05~0.2mm、径方向に約0.03mm以下ほどになります。寸法の厳しい加工では影響が出るため、注意が必要です。加工寸法を優先する場合はピン角の方が高精度な加工ができます。
以上のことから、
アタリ付きは
・ねじれが40度以上のエンドミル
・硬い被削材を加工する場合
ピン角は
・ねじれの弱いエンドミル
・非鉄を加工する場合
・加工寸法が厳しい場合
と、状況に合わせて選択するといいです。
>>エンドミルにねじれ角がある理由とは?直刃との違い、メリット・デメリットについて解説!
>>エンドミルの寿命を判定する方法とは?再研磨に出すべきタイミングを徹底解説!
アタリ付きエンドミルの事例:先端16mm 超硬 ヘッド交換式4枚刃ラフィングエンドミルの再研磨
こちらは当社で手掛けた、先端16mmのヘッド交換式ラフィングエンドミルの再研磨事例の一つです。
粗削り用のラフィングエンドミルのコーナーはギャッシュを当てた「あたり付き」にしてあります。
ピン角エンドミルの事例:先端12mm 超硬 4枚刃スクエアエンドミルの再研磨
こちらは当社で手掛けた、先端12mmのエンドミルの再研磨事例の一つです。
ねじれ30度のこのエンドミルのコーナーは「ピン角」にしてあります。
切削工具の寿命診断&再研磨は、再研磨.comにお任せください!
再研磨.comを運営する株式会社宮本製作所では、焼結金属と呼ばれる非常に硬い素材の加工を行っており、その過程で得た加工に関するノウハウを活かし、工具の再研磨を行っています。
再研磨.comでは、ドリルやエンドミル、リーマ等の切削工具を高い品質で再研磨するため、最新の加工設備や検査設備を取り揃えています。当社の再研磨は、職人が手作業で行う再研磨とは異なり、繰り返しの精度が高い、安定した品質での再研磨加工を可能としています。
当社は、お客様が使用済みの工具を再研磨加工することで、刃物そのものの延命化を実現します。一般的に再研磨のコストは、工具購入コストの1/5~1/10程度です。そのため、お客様のコスト削減に大きく貢献することができます。
また、従来の切削では無理があった箇所を修正し、負荷を軽減することで、より多くの切削が可能となる刃物を提供します。ただ工具を再研磨するだけでなく、作業の効率化を図ることができる低コスト工具の提供を行っています。
さらには規格品よりも、高精度の加工をより少ない工程で加工を実現する工程集約工具への改造にも対応しています。
【再研磨の匠にしかできない技を、貴社の刃物に】
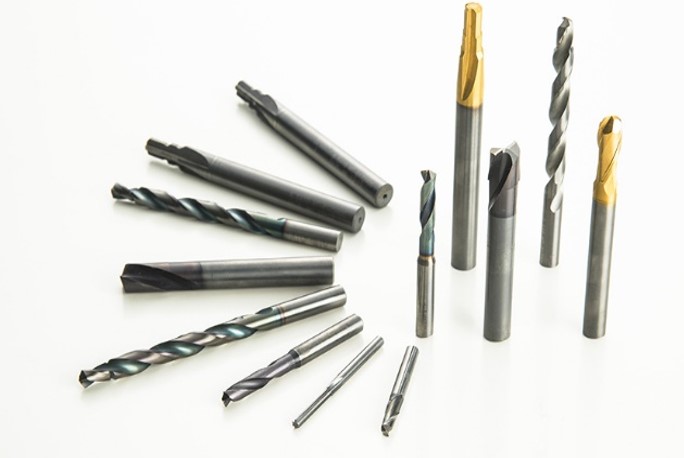
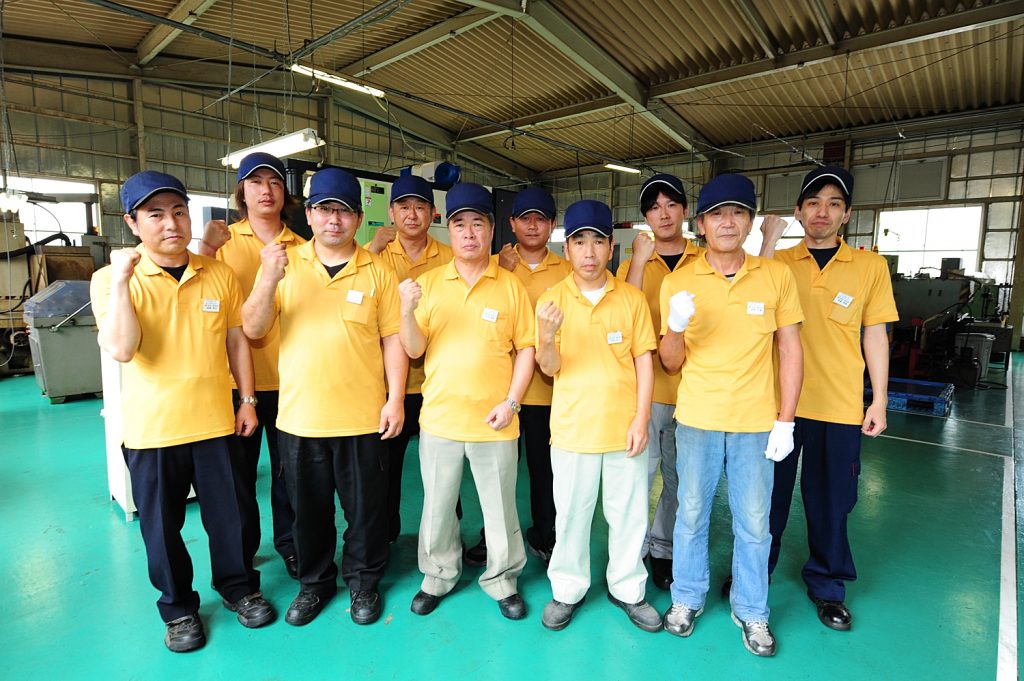
切削加工会社である当社が、片手間で行う事業ではなく、工具研磨専用の加工設備・検査設備を取りそろえておこなっている、本気の再研磨です。そのため、どこにも負けない品質で工具の再研磨加工を行うことをお約束いたします。当社は、「再研磨の匠にしかできない技を、貴社の刃物に。」を合言葉に、一本一本の再研磨に魂を込め、お客様を“工具”からサポートいたします。
ドリルやエンドミル、リーマなどの切削工具の再研磨を検討されている方は、まずは再研磨.comへお気軽にご相談ください。